What is Porosity in Welding: Typical Resources and Efficient Solutions
Wiki Article
The Science Behind Porosity: A Comprehensive Overview for Welders and Fabricators
Comprehending the intricate systems behind porosity in welding is critical for welders and producers pursuing flawless workmanship. As metalworkers explore the midsts of this sensation, they discover a world regulated by various aspects that influence the development of these tiny gaps within welds. From the structure of the base products to the ins and outs of the welding procedure itself, a wide variety of variables conspire to either worsen or reduce the existence of porosity. In this extensive overview, we will certainly decipher the scientific research behind porosity, exploring its results on weld high quality and introduction progressed methods for its control. Join us on this journey with the microcosm of welding flaws, where precision satisfies understanding in the pursuit of perfect welds.Recognizing Porosity in Welding
FIRST SENTENCE:
Examination of porosity in welding discloses important understandings into the stability and top quality of the weld joint. Porosity, identified by the visibility of dental caries or gaps within the weld metal, is a common worry in welding procedures. These spaces, if not correctly dealt with, can jeopardize the structural stability and mechanical residential or commercial properties of the weld, resulting in possible failures in the finished product.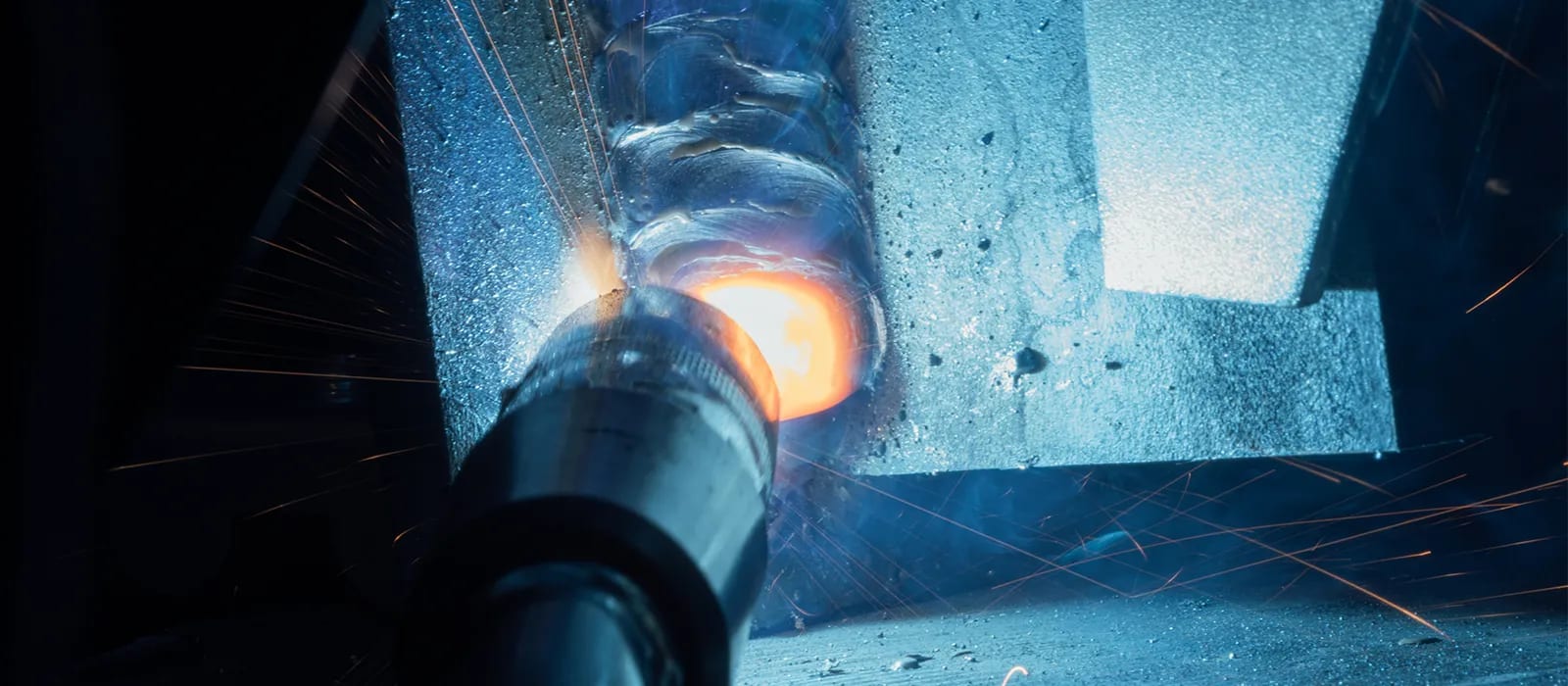
To identify and evaluate porosity, non-destructive screening methods such as ultrasonic testing or X-ray inspection are frequently used. These techniques permit the identification of interior issues without jeopardizing the integrity of the weld. By analyzing the size, form, and distribution of porosity within a weld, welders can make educated decisions to boost their welding procedures and accomplish sounder weld joints.
Factors Influencing Porosity Development
The event of porosity in welding is influenced by a myriad of elements, varying from gas protecting efficiency to the details of welding parameter setups. Welding parameters, including voltage, current, take a trip speed, and electrode type, likewise influence porosity development. The welding method utilized, such as gas metal arc welding (GMAW) or secured metal arc welding (SMAW), can affect porosity development due to variants in warm distribution and gas insurance coverage - What is Porosity.Effects of Porosity on Weld Quality
Porosity formation dramatically jeopardizes the architectural integrity and mechanical properties of welded joints. When porosity exists in a weld, it develops gaps or dental caries within the product, reducing the total strength of the joint. These spaces serve as stress focus factors, making the weld a lot more susceptible to fracturing and failing under lots. The presence of porosity likewise weakens the weld's resistance to deterioration, as the caught air or gases within deep spaces can react with check that the surrounding setting, causing degradation in time. Additionally, porosity can hinder the weld's ability to withstand stress or impact, further endangering the general top quality and reliability of the welded structure. In important applications such as aerospace, auto, or structural constructions, where safety and toughness are paramount, the damaging results of porosity on weld top quality can have extreme repercussions, stressing the relevance of decreasing porosity through appropriate welding methods and treatments.Techniques to Lessen Porosity
To boost the high quality of welded joints and make sure architectural honesty, welders and fabricators use details strategies aimed at lowering the development of see page gaps and dental caries within the product during the welding process. One efficient approach to minimize porosity is to guarantee appropriate product preparation. This includes extensive cleaning of the base steel to get rid of any contaminants such as oil, oil, or moisture that might add to porosity formation. Furthermore, utilizing the suitable welding specifications, such as the right voltage, existing, and take a trip speed, is vital in protecting against porosity. Preserving a regular arc length and angle throughout welding additionally aids lower the chance of porosity.
Making use of the suitable welding strategy, such as back-stepping or using a weaving motion, can also assist distribute warm uniformly and lower the chances of porosity formation. By executing these strategies, welders can properly lessen porosity and generate premium welded joints.

Advanced Solutions for Porosity Control
Executing innovative technologies and ingenious methods plays a crucial duty in achieving superior control over porosity in welding procedures. Furthermore, employing advanced welding methods such as pulsed MIG welding or modified atmosphere welding can also help minimize porosity problems.Another More Bonuses advanced option includes using sophisticated welding tools. For instance, utilizing equipment with integrated features like waveform control and advanced source of power can enhance weld high quality and reduce porosity risks. The execution of automated welding systems with accurate control over specifications can substantially reduce porosity issues.
Moreover, including advanced tracking and inspection innovations such as real-time X-ray imaging or automated ultrasonic testing can aid in detecting porosity early in the welding process, enabling prompt restorative actions. Overall, integrating these innovative options can considerably improve porosity control and boost the overall top quality of welded elements.
Final Thought
Finally, comprehending the science behind porosity in welding is vital for welders and producers to create top quality welds. By identifying the aspects influencing porosity development and executing strategies to lessen it, welders can boost the total weld top quality. Advanced solutions for porosity control can better enhance the welding process and ensure a strong and reliable weld. It is essential for welders to continuously enlighten themselves on porosity and execute best practices to achieve optimum outcomes.Report this wiki page